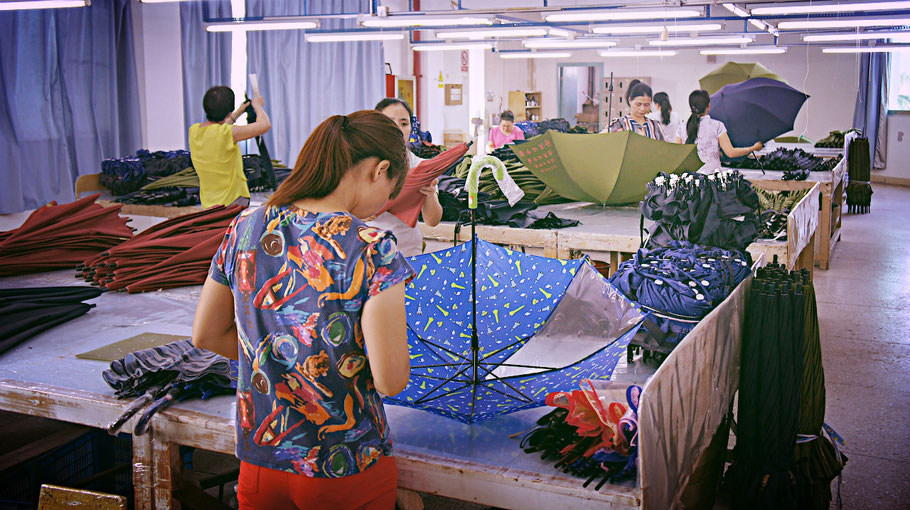
アンベル株式会社では、日々不良率をどう下げるかを考えています。
しかし実際は不良率を下げることはすごく難しく、簡単ではありません。
海外縫製工場は「安かろう悪かろう」がほぼあてはまる
不良率を下げていくには、まず協力取引工場の選定が大切です。入口で間違えてしまうと不良率はなかなか下がりません。
傘の製造は中国がほとんどですが、一口に中国といっても色々な工場があります。品質により、Aランク・Bランク・Cランク…の工場があり、当然品質のよい工場はコストも高くなりますが、いかなる理由があっても品質Aランクの工場一択で選定をするべきだと弊社は考えます。
Bランクの工場を指導し品質向上を狙う方もいらっしゃいますが、満足出来る品質になったころにはコストもAランクに上がってしまい、何の為に指導したのか…ということになってしまいます。
新規取引する工場で見積りする際に、破格に安い値段を提示された場合は、「これは儲かるな」と喜ぶ前に品質に問題がないかのチェックが必要です。
意外とチェックが緩い材料検品
工場選定が終わったら、どんな検品フローを経由して最終製品になるかを把握しなければなりません。
意外とスルーされているのが、材料検品です。
サプライヤーから仕入れた生地・骨・ハンドルなどパーツの全量検品を行っているか要チェックです。
Bクラス工場のほとんどは抜き取り検品で留めているところが多く、抜き取り検品においても「何本不良が出たらサプライヤーに返却する」など明確な基準が定められていない工場がほとんどです。
不良率を下げるためにも、そもそも不良要因になる材料を製造ラインに流さない、良品のみを流すというスタンスが大切だと思います。
時間と人員を最もさくべきなのは中間検品
各工程から順次半製品になっていき、ハンドルを取り付ける工程が一番最後になります。
その最終工程の一歩手前に行う検品が中間検品(半製品検品)です。
私の経験上、この中間検品工程で検品と手直しにじっくり手間をかけている工場ほど不良率が低い傾向にあります。
理由は一旦ハンドルを取り付けてしまった後で不良を発見し、手直しをしたとしても、その手直し工程において、ハンドルが傷ついて二次的な不良が出てしまったり、ハンドルが付いていることで補修作業がやりにくくなってしまうからです。
最後の砦は外部検品会社による検品
中間検品の後はハンドルやラベルなどを取り付けて完成品になります。その後は最終検品になります。
当然ながらAランク・Bランク工場は最終検品を実施していますが、Cランク工場は最終検品を実施していなかったり、記録がなかったりしますので要注意です。
ただ最終検品といっても、同じ工場内でのことですで、どうしても自社の商品の検品には甘さが出てしまうことがあります。
完璧にとはいいませんが、ほぼ不具合がない商品を目指す場合は最終検品が終わった後、さらに外部検品会社による検品を推奨します。特に自称「品質には自信があります」と言うBクラスの工場で外部検品を実施すると、不良率が高かったりしますから、その乖離が大きい場合は工場と検品会社ですり合わせ→不良原因追求→改善といったPDCAが必要になります。
検品だけでは不良率を下げられない
最後に、時間の経過による不良という問題があります。わかりやすい例を書きますと、錆やめっき不良などの問題です。
めっきは工場出荷時には非常に綺麗な状態ですが、半年ほど経過しますと黒変(黒い斑点状のもの)したりで、時間が経過しないと判明しない不良があります。こればかりは目視による検品での判断は難しく、そもそも良い材料で作っているか?という部分が問われます。
不良率を下げていくには応分のコストが必要で、良い工場・良い材料を組み合わせて初めて成立すると考えます。
時々「品質よく、価格は安く」という理念を掲げている工場を見ますが、現実にそれが実行出来るのは単一商品を大量に作れる工場だけです。やはり品質良いものを作るには、それ相応のコストが必要になるのではないでしょうか。