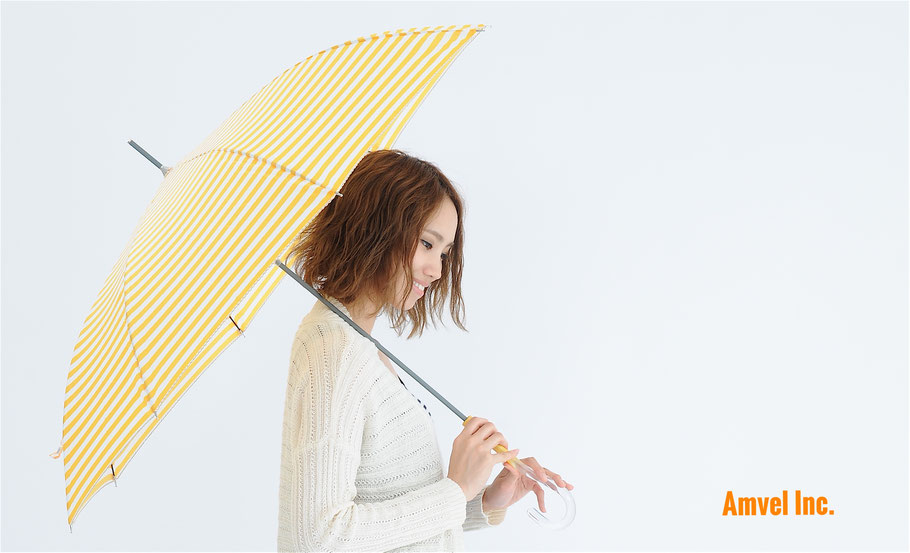
傘をデザインする際、何よりも傘生地にどのようなプリントデザインを施すかで仕上がりが大きく変わってくると思います。
今回のブログでは「傘生地のプリントは最大は何色使えるか?」という質問がありましたので説明していきたいと思います。
傘生地のプリントは手法よって異なる
傘生地のプリントと言っても、施すプリント方法によっても違いがあります。
よく使われる手法は以下の4通りです。
- オートプリント
- シルクスクリーンプリント
- 転写プリント
- デジタルインクジェットプリント
まずは、それぞれのメリット・デメリットを説明します。
①オートプリント
傘のプリント方法として最も使われているのが、このオートプリントになります。
酸性染料を用いたプリント方法で、ポリエステルなどの合成繊維において大量生産する場合によく使われます。
【メリット】
- 一旦デザイン版やカラーが確定すれば、安定した品質で傘生地の大量生産が可能です。
【デメリット】
- 大量生産向けの作り方になりますので、発注ミニマムがあり少量生産には不向き。
- 量産が終わるまでは仕上がりイメージが確認出来ないので、一定の経験や感が必要。
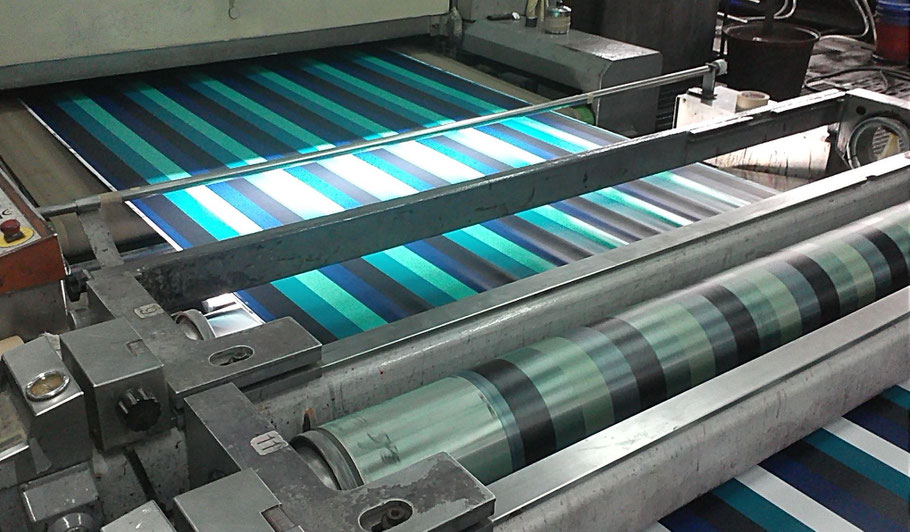
②シルクスクリーンプリント
Tシャツのプリントする方法としてはポピュラーな手法。
プリント台にセットした傘生地の上に版を置き、インクを刷込みます。
昔は版のメッシュ素材としてシルクが使われていた事から、シルクスクリーンプリントと呼ばれていますが、現在はポリエステル素材を用いているのが殆どだと思います。
【メリット】
- 小ロットでの生産向きで、デザイン版や色の確認もスピーディーに対応可能。
- ブランドロゴなどのワンポイントプリントに最適。
【デメリット】
- 傘生地に対し、プリント面積比率が大きいと皺が出やすい。
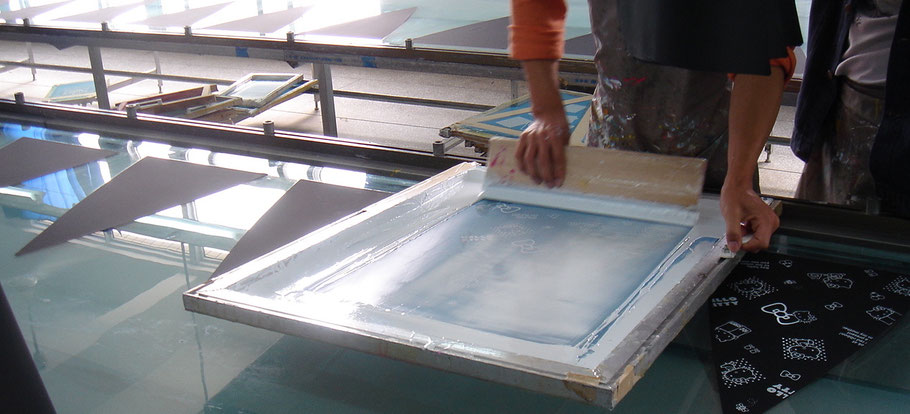
③転写プリント
インクジェットプリンターで出力した紙を基に、傘生地へ熱圧着し転写する方法。
【メリット】
- 極論1本から製造可能でオートプリント量産前のサンプル確認として利用する事が多い。
- 色数に関係なくプリントが可能。
【デメリット】
- 非常に手間がかかり、量産には向きません。
- 堅牢度が高くないので、経年劣化や保存状態により色落ちする。

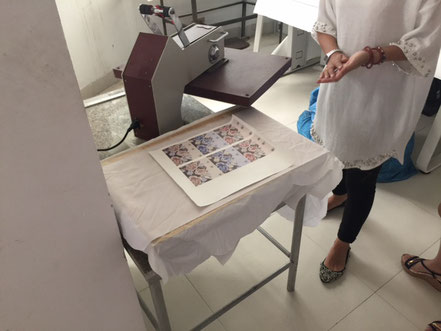
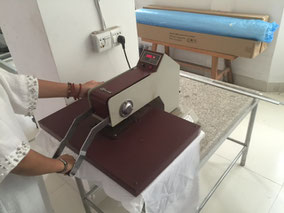
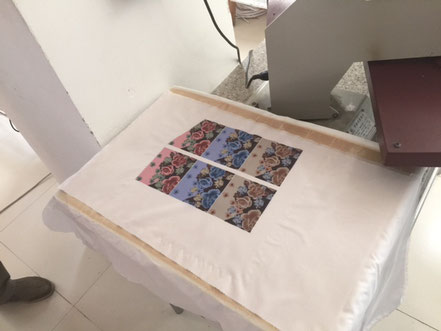
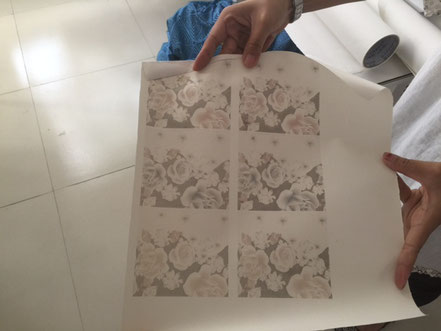
④デジタルインクジェットプリント
最近アパレルでも小ロット生産の際にはよく利用されている方法。
パソコンのインクジェットプリンターと同じ理屈で、生地に直接プリントする方法。
【メリット】
- 小ロットで製造可能で、一定の堅牢度もある。
- 色数に関係なくプリントが可能。
【デメリット】
- 非常にコスト高で一般化するまでは、まだまだ時間がかかる。
- 製造の工程上やむを得ないが、プリントの斜行が発生しやすい。チェックやボーダーなどの規則正い柄には不向き。
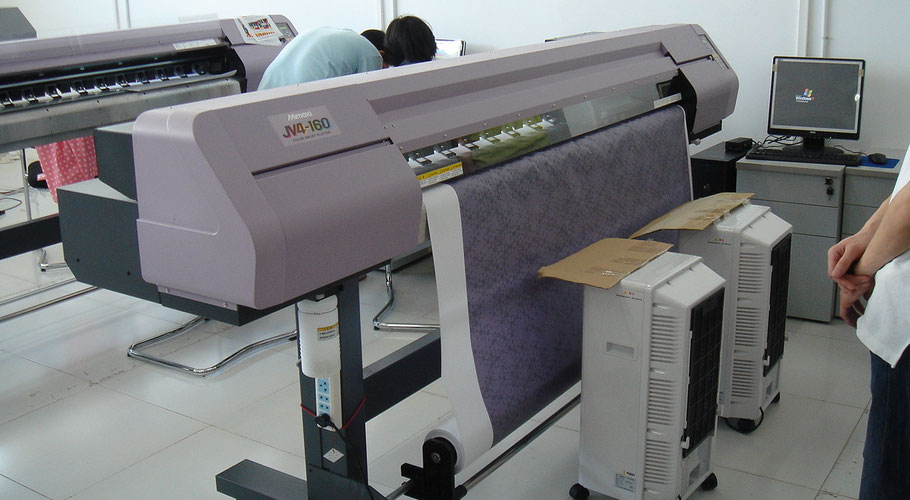
まとめ
タイトルにある「傘生地のプリントの最大色数は?」ですが、
- オートプリントは最大15色まで。
- シルクスクリーンプリント・転写プリント・デジタルインクジェットプリントは無制限。
ただ実際製造するには様々な制限や注意すべき事がありますので、傘のOEMで検討中のお客様はアンベルへご相談下さい。